CNC Lathe Parts Factories: Revolutionizing Metal Fabrication
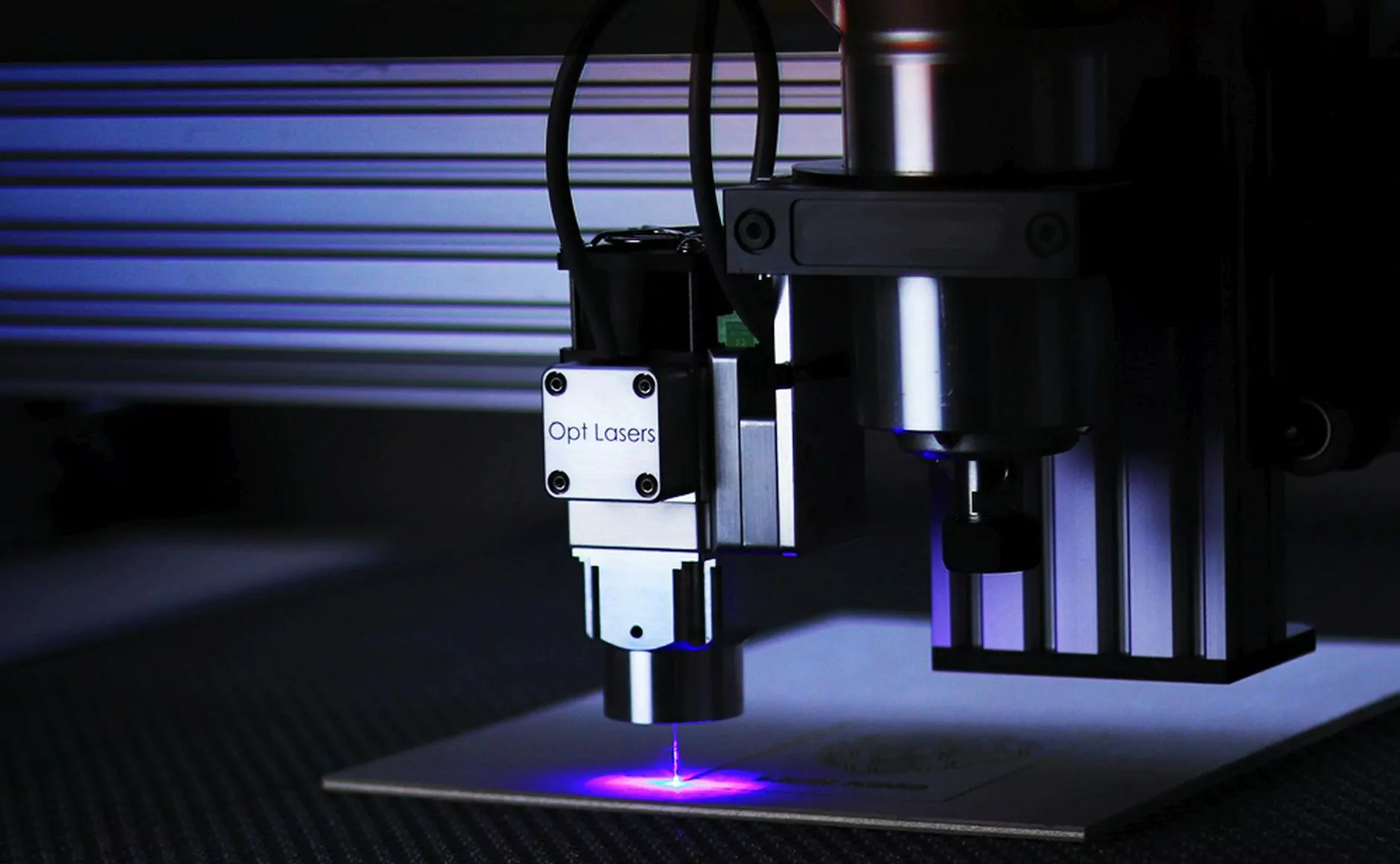
Introduction to CNC Lathe Parts Factories
The landscape of modern manufacturing is rapidly evolving, and CNC lathe parts factories are at the forefront of this transformation. These facilities utilize Computer Numerical Control (CNC) technology to manufacture precision parts for various industries, including aerospace, automotive, and medical devices. With their ability to produce high-quality components with intricate designs efficiently, CNC lathe parts factories play a crucial role in today's industrial supply chain.
Understanding CNC Technology
CNC technology is a groundbreaking approach to machining that allows for remarkable precision and efficiency. Unlike traditional methods, CNC machines operate using programmed commands that control various machine tools. This programming results in repeatable and accurate movements that enhance productivity while minimizing human error.
Some key elements of CNC technology include:
- Automation: CNC machines can operate independently with minimal human intervention, allowing manufacturers to increase output rates.
- Precision: The precision of CNC machines leads to better tolerances, ensuring that products meet stringent quality standards.
- Flexibility: CNC machines are versatile and can be reprogrammed quickly for different designs, making them ideal for custom projects.
The Role of CNC Lathe Parts Factories
CNC lathe parts factories are specialized manufacturing facilities focused on creating complex components using CNC lathe machines. Lathes are particularly effective for creating cylindrical shapes, such as shafts, pulleys, and fittings. The significance of these factories in metal fabrication cannot be overstated.
They provide various services, including:
- High-Volume Production: Capable of producing large quantities of parts in a short period.
- Custom Engineering: Tailored designs to meet specific client requirements.
- Material Variety: Utilization of various materials, including metals, plastics, and composites, to create diverse products.
Benefits of Partnering with CNC Lathe Parts Factories
Choosing to work with CNC lathe parts factories offers numerous advantages for businesses:
- Cost Efficiency: CNC manufacturing often results in reduced costs per unit due to the high efficiency and rapid production speed.
- Quality Assurance: Automated processes ensure consistent quality standards across all parts produced.
- Enhanced Innovation: With the capability to produce intricate designs, businesses can explore innovative product designs without the constraints of traditional machining.
- Scalability: As demand grows, CNC factories can quickly adjust production levels to meet market needs.
Applications of CNC Lathe Parts
The applications of parts produced by CNC lathe factories are vast and varied. Here are some key industries where CNC lathe parts play a critical role:
Aerospace Industry
Components such as turbine housings, brackets, and fittings are often produced with CNC lathes due to their high precision and ability to work with lightweight materials.
Automotive Industry
CNC lathe parts are used in manufacturing gears, axles, and engine components, which require a high degree of accuracy and reliability.
Medical Devices
In the medical field, CNC lathe parts can be found in surgical instruments, implants, and other devices that demand strict adherence to quality standards.
Consumer Electronics
Many components in smartphones and laptops are produced using CNC technologies, highlighting the importance of lathe parts in high-tech applications.
Quality Control in CNC Lathe Parts Manufacturing
Quality control is a critical aspect of CNC lathe parts factories. Manufacturers implement rigorous quality assurance processes to ensure that every part produced meets the necessary standards:
- In-Process Inspection: Regular checks during the manufacturing process to catch any deviations early.
- Final Inspection: Each batch of parts undergoes a thorough inspection before shipping.
- Quality Certifications: Many factories seek ISO certification to showcase their commitment to quality in all aspects of manufacturing.
The Future of CNC Lathe Parts Factories
As technology continues to evolve, CNC lathe parts factories are poised for exciting advancements. The integration of Industry 4.0 technologies, such as IoT and AI, is likely to enhance productivity and efficiency further:
- Smart Manufacturing: Factory floors will become increasingly interconnected, allowing for real-time monitoring of production processes.
- Predictive Maintenance: Utilizing analytics to predict when machines will require maintenance, thereby reducing downtime.
- Advanced Materials: The exploration of new materials and composites that can be machined using CNC technology will open new avenues for innovation.
Choosing the Right CNC Lathe Parts Factory
When selecting a CNC lathe parts factory, businesses should consider several critical factors to ensure they partner with a quality manufacturer:
- Experience: Look for a factory with a proven track record in your specific industry.
- Technological Capabilities: Ensure the factory has the necessary modern CNC machines and technology.
- Client Testimonials: Check reviews and references from previous clients to gauge satisfaction and reliability.
- Customization Options: Confirm that the factory can handle custom designs and unique specifications.
Conclusion
In conclusion, CNC lathe parts factories are essential to modern manufacturing, providing businesses with unparalleled precision, efficiency, and quality. By leveraging CNC technology, these factories have revolutionized the production of metal parts, enabling industries to innovate and grow. As we look to the future, the continued advancement of CNC technologies will likely unlock even more possibilities for manufacturing excellence. Partnering with a reputable CNC lathe parts factory may very well be the key to staying competitive in a fast-paced market.